Discover detailed applications of eddy current, including industrial testing, braking systems, and material sorting. Learn how eddy current testing enhances safety and efficiency.
Introduction
Eddy currents are circulating electrical currents induced within conductors by a changing magnetic field, as explained by Faraday’s Law of Electromagnetic Induction. These tiny loops of current flow in closed paths inside the conductor, perpendicular to the magnetic field, much like swirling water flowing around a rock in a stream. The induced currents generate opposing magnetic fields, which form the basis of many practical applications.
Eddy currents have diverse uses, including electromagnetic braking, induction heating, metal detectors, and non-destructive testing, making them essential in both electrical engineering and everyday technology. This article explores the industrial applications of eddy current testing across power plants, manufacturing, and transportation sectors.
Principles of Eddy Currents
Eddy currents are swirling loops of electric current that form inside conductors when they are exposed to a changing magnetic field. This phenomenon is governed by Faraday’s Law of Electromagnetic Induction, which explains that a time-varying magnetic field in a conductor creates an electromotive force (EMF)—a kind of electrical push. When this EMF flows within the body of a conductive material, it forms circular electric currents known as eddy currents.
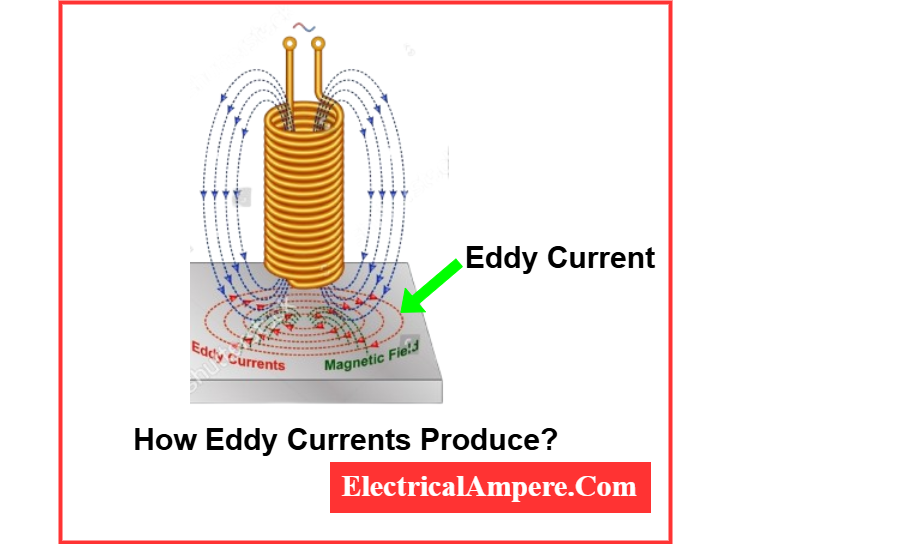
According to Lenz’s Law, these eddy currents create magnetic fields that oppose the original change in magnetic flux. This opposing effect results in energy being lost as heat, but it also enables useful applications such as eddy current braking, induction heating, and non-destructive testing.
Understanding these principles is vital to control, reduce, or enhance eddy currents in industrial and technological applications.
Factors Affecting Eddy Current Formation
Several key factors influence the strength and behavior of eddy currents:
- Rate of Change of Magnetic Field: Faster changes induce stronger eddy currents.
- Material Conductivity: Higher conductivity materials (like copper or aluminum) allow larger eddy currents.
- Thickness of the Conductor: Thicker materials enable more extensive current loops, increasing eddy current strength.
- Magnetic Field Intensity: A stronger magnetic field generates more intense eddy currents.
- Shape and Geometry: The geometry of the conductor affects the distribution and path of eddy currents.
- Presence of Laminations: Laminated or slotted structures reduce eddy current paths, minimizing energy losses (as used in transformer cores and motor rotors).
- Skin Effect: Eddy currents tend to concentrate near the surface of conductors at higher frequencies, reducing penetration depth. This phenomenon, known as the skin effect, limits how deeply eddy currents can penetrate, impacting applications like heating and testing.
Applications of Eddy Currents
The following are the applications of eddy currents.
- Crack Detection
- Condenser Tube Inspection
- Pipes & Tubes Testing
- Wire Testing
- Material Sorting
- Weld Testing
- Coating Thickness Measurement
- Eddy Current Braking Systems
- Induction Heating
- Electromagnetic Damping
The industrial applications of eddy current testing span from material testing to advanced quality control systems.
1. Crack Detection
Eddy current is used to detect the surface breaking cracks in the ferrous and non-ferrous. The high-frequency eddy current is used to find cracks in ferrous materials. And low-frequency eddy current is used to detect the cracks in the no-ferrous materials.
The subsurface cracks in ferrous materials can also be detected with the use of eddy currents, but the materials need to be magnetically saturated to remove the permeability effect. Eddy currents are most useful for the detection of surface cracks.
The small probe is used in high frequencies that cover a large area; it takes a long time. The frequencies of the order 2 MHz give high resolution.
Low-frequency crack detectors have a larger probe that allows suitable coil inductances. The low frequency is used as per the requirement of depth of eddy current penetration. The range of low frequencies is between 100Hz to l00kHz.
2. Condenser Tube Inspection
Eddy current testing is a widely used non-destructive testing (NDT) method for inspecting condenser tubes. It is especially effective in heat exchangers where detecting surface and near-surface defects is crucial. The testing equipment includes a probe or coil, signal generator, and receiver. The probe is inserted into or placed near the tube’s inner or outer surface, and an alternating current from the signal generator induces eddy currents within the tube wall.
As the probe moves along the tube at a controlled speed, it detects changes in eddy current behavior caused by variations in conductivity, thickness, corrosion, cracks, pitting, or wall thinning. These disruptions indicate potential flaws and are recorded for analysis. This non-contact method allows for fast, accurate assessment without dismantling the system, making it especially valuable in power plants, refineries, and nuclear facilities where early detection of minor defects prevents costly shutdowns and maintains condenser efficiency.
3. Pipes &Tubes Testing
Beyond condensers, eddy current testing is applied to various industrial pipes and tubes used in refineries, nuclear plants, and chemical industries. This testing identifies flaws such as cracks, corrosion, and wall thinning in these tubes. The probes may be inserted inside the tubes, and different frequencies are used to detect defects at varying depths, ensuring early detection and preventing catastrophic failures. Variations in thickness, conductivity, or flaws like cracks disrupt the current flow—these anomalies are recorded and analyzed to detect defect
4. Wire Testing
In wire testing, the wire is usually kept stationary while a rotating probe or coil moves along its length. This setup induces eddy currents in the wire’s surface. The probe detects changes caused by defects such as surface cracks, corrosion, or diameter variations. By identifying these anomalies early, the test helps ensure the wire’s structural integrity and performance without damaging it.
5. Material Sorting
Eddy current separators are widely used in recycling plants to sort non-ferrous metals—metals that don’t contain iron and behave differently when exposed to magnetic fields—such as aluminum, copper, and brass from mixed waste. These separators induce circulating currents in metals when passed through a magnetic field, which in turn generates repelling forces that push these metals away from other materials.
In industries like aerospace and automotive manufacturing, eddy current sorting helps distinguish between different metal alloys— mixture of two or more metals often designed to have specific properties — based on their electrical conductivity. This ensures that components with precise material properties are selected, which is crucial for safety and performance standards.
The electronics industry also uses this technique to sort tiny components such as capacitors, inductors, and connectors, enhancing assembly accuracy and efficiency.
Even in daily operations like banking, coin-sorting machines utilize eddy currents to detect and separate coins based on their metal composition. Each metal type responds differently to magnetic fields, allowing for fast and accurate sorting.
Additionally, eddy current sorting can assess material thickness and detect the presence of surface coatings like paint or plating. This is especially useful in industries where consistency in surface treatment or structural integrity is essential.
6. Weld Testing
Eddy current testing is widely used to inspect welds for various surface and near-surface defects, providing a fast, non-contact, and non-destructive evaluation method. It is highly sensitive to detecting flaws such as:
- Cracks: Surface and near-surface cracks within welds are effectively detected.
- Porosity: Voids, gas pockets, and other forms of porosity inside the weld can be identified.
- Lack of Fusion: Incomplete fusion between weld layers or between the weld and base material is detectable.
- Weld Voids: Voids or gaps within the weld structure can be revealed.
This method works by inducing eddy currents in the weld area, where any disruptions in current flow indicate potential defects. Eddy current testing often complements other inspection techniques such as radiographic testing (RT) and ultrasonic testing (UT). While RT and UT are well-suited for detecting internal flaws, eddy current testing excels at identifying surface and shallow subsurface defects, making it an essential part of a comprehensive weld inspection program.
7. Coating Thickness Measurement
Eddy current testing is an effective method for measuring the thickness of non-conductive coatings applied on conductive substrates. This works because the coating changes the distance between the probe and the conductive base material, affecting the flow of eddy currents induced in the substrate. Since eddy currents are sensitive to changes in conductivity and proximity, variations in coating thickness alter the eddy current response, allowing precise measurement without damaging the surface. This technique is widely used to ensure quality control in industries like aerospace, automotive, and manufacturing.
8. Eddy Current Braking Systems
The eddy current braking system advantages include non-contact operation, reduced maintenance, and silent braking in high-speed trains and roller coasters. Common uses also include industrial machinery, where precise speed control and emergency stopping are crucial.
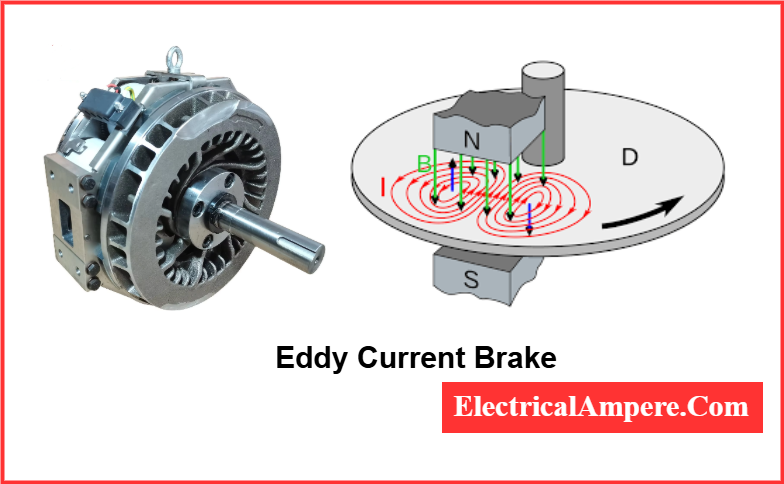
Eddy current braking is one of the most practical and fascinating applications of electromagnetic principles. Following the use of eddy currents in crack detection and material testing, they are also widely employed in modern braking systems—particularly in high-speed trains, elevators, and amusement park rides.
In this application, a conductive metal disc or rail moves through a magnetic field generated by permanent magnets or electromagnets. As the disc cuts through the magnetic lines of force, circulating eddy currents are induced within it. According to Lenz’s Law, these currents create their own magnetic fields that oppose the original motion of the conductor. This opposition results in a braking force that slows down or stops the moving object without any physical contact.
The main advantage of this system is its wear-free operation. Since there are no frictional components, the brake doesn’t degrade over time like traditional mechanical brakes. Additionally, eddy current braking provides smooth and quiet deceleration, which is ideal for scenarios where sudden stops could cause discomfort or mechanical stress.
However, it’s worth noting that eddy current brakes are most effective at high speeds. As the speed decreases, the strength of the induced eddy currents diminishes, reducing the braking force. For this reason, they are often used in combination with other braking systems in vehicles and machinery.
Eddy current braking is a brilliant example of how a non-contact method can offer precise, efficient, and low-maintenance solutions in modern engineering systems.
9. Induction Heating
After exploring the use of eddy currents in braking systems, it’s important to highlight another major industrial application—induction heating. This method harnesses eddy currents to heat conductive materials quickly and efficiently without direct contact.
In induction heating, a high-frequency alternating current flows through a coil, generating a rapidly changing magnetic field around it. When a conductive material, such as a metal rod or billet, is placed within this magnetic field, eddy currents are induced within the material. These circulating currents encounter resistance as they flow, and this resistance converts electrical energy into heat directly within the object.
Induction heating technology is applied in two main forms: induction heaters and induction furnaces. Induction heaters are commonly used for surface hardening, brazing, and soldering, where rapid, localized heating is required. On the other hand, induction furnaces use similar principles to melt metals by generating intense eddy currents.
What makes induction heating particularly effective is its localized and controlled nature. Unlike conventional heating methods, which rely on convection or conduction and heat the surface first, induction heating allows for precise and uniform heating of the target material. This precision is especially valuable in processes like metal hardening, annealing, soldering, and forging.
Moreover, since there is no physical contact between the coil and the material being heated, there’s minimal wear and maintenance. The system also heats up very rapidly, improving energy efficiency and productivity in industrial environments.
However, induction heating is best suited for electrically conductive materials, and the initial setup cost can be high due to the equipment and power supply requirements. Still, the long-term benefits in speed, cleanliness, and process control make it a go-to choice in many modern manufacturing operations.
10. Electromagnetic Damping
Eddy currents play a crucial role in electromagnetic damping, where they provide smooth, contactless resistance to reduce unwanted vibrations or oscillations in mechanical systems. When a conductor moves through a magnetic field, circulating currents are induced, converting kinetic energy into heat and slowing the motion. This principle is widely used in precision instruments, galvanometers, and measuring devices to stabilize needle movements and improve accuracy.
Advantages of Eddy Current Testing
1. Non-Destructive Nature
Eddy current testing allows for inspection without damaging the tested material.
2. High Sensitivity to Surface Defects
It effectively detects cracks, pits, and other surface anomalies.
3. Rapid Inspection Capabilities
The method provides quick results, ideal for mass or continuous inspection.
Limitations of Eddy Current Testing
1. Limited Depth of Penetration
It is mostly sensitive to surface and near-surface defects only.
2. Limited to Conductive Materials
Only metals and conductive materials can be tested.
3. Sensitivity to Surface Conditions
Surface roughness, coatings, or cleanliness may affect accuracy.
Conclusion: Summary of Eddy Current Applications
Eddy current applications span a wide range of industries, from power plants and recycling facilities to aerospace and transportation systems. As a non-destructive testing method, eddy current testing offers fast, accurate, and contactless inspection of conductive materials, making it especially useful for detecting surface and near-surface defects.
Moreover, eddy current braking system advantages—such as silent operation, low maintenance, and high reliability—have made them essential in modern transportation, including high-speed trains and amusement park rides. Similarly, eddy current sorting systems are critical in recycling, helping to efficiently separate non-ferrous metals and ensure quality in material reuse.
Despite limitations like shallow penetration and the need for conductive materials, the technique continues to evolve with new sensor technologies and automation. Eddy current testing remains a vital inspection tool, supporting industries that rely on precision, safety, and speed.
From material inspection to high-speed transportation, innovations in eddy current technology underline its growing relevance in safety-critical sectors and sustainable industrial practices.
Looking ahead, advances in sensor technology, artificial intelligence, and automated defect analysis promise to further enhance the accuracy, efficiency, and scope of eddy current applications across industries.
Frequently Asked Questions (FAQs)
Eddy current is a circular electric current induced in a conductor when it is exposed to a changing magnetic field. This is based on Faraday’s law of electromagnetic induction.
Eddy currents are widely used in non-destructive testing, induction heating, metal sorting, eddy current brakes, and surface crack detection in various industrial sectors.
In eddy current braking systems, magnetic fields induce circulating currents in metal parts (like a disc or rail), creating a magnetic force that resists motion and slows down moving objects without physical contact.
Eddy current testing is fast, accurate, and does not require physical contact, making it ideal for detecting surface cracks and material defects in critical applications like aerospace and nuclear industries
Eddy currents only work with conductive materials and have limited penetration depth, making them unsuitable for detecting deeper flaws or testing non-metallic materials
Read Next: