A DC machine is an electromechanical device that operates either as a motor or a generator, converting mechanical energy into direct current (DC) electrical energy or converting electrical energy into mechanical energy. It works on the principle of electromagnetism, where a magnetic field interacts with a current-carrying conductor, causing motion (in the case of a motor) or generating electricity (in the case of a generator).
Industrial applications that require precise control of speed and torque, such as electric vehicles, industrial machinery, and robotics, widely use DC machines. Due to their efficiency and control capabilities, DC machines have maintained their importance in various fields, despite the rise of AC machines.
Types of DC Machines
We can categorize the DC machines based on their function into two main types:
- DC Motor: A DC motor converts electrical energy into mechanical energy. It works by utilizing the interaction between the magnetic field generated by the field windings (or magnets) and the current flowing through the armature windings. The result is mechanical motion. DC motors are used in applications requiring adjustable speed and torque control, such as electric vehicles, elevators, industrial tools, and robotics. Their ability to provide smooth speed control makes them ideal for tasks that require precision.
- DC Generator: A DC generator operates by converting mechanical energy into electrical energy. When the mechanical force from a turbine or engine rotates the armature within a magnetic field, it induces a voltage across the armature windings. DC generators often produce DC power for specific tasks such as battery charging, electrochemical processes, or when certain equipment or systems require DC power.
Each type of DC machine plays a significant role in the fields of transportation, manufacturing, and power generation, offering versatile control and high efficiency.
Structure of a DC Machine
Several key components of a DC machine, each serving a specific function are as follows.
- Stator: The stator is the stationary part of the DC machine and is responsible for producing the magnetic field. It typically consists of either electromagnets (field windings) or permanent magnets. The strength and orientation of the magnetic field generated by the stator are critical for the machine’s operation, as it interacts with the armature to produce mechanical motion or generate electricity.
- Rotor (Armature): The rotor, or armature, is the rotating part of the DC machine. In a motor, it is where the current-carrying conductors interact with the stator’s magnetic field to produce rotational motion. In a generator, the rotor turns to cut through the magnetic field, inducing an electromotive force (EMF) that generates current in the armature windings. The armature has multiple coils of wire arranged to maximize the interaction with the magnetic field.
- Commutator: The commutator is a mechanical switch attached to the rotor. Its primary function is to reverse the current flowing through the armature windings at the right moments, ensuring that the torque in motors or the voltage output in generators stays unidirectional. Without the commutator, the current direction would reverse with each half rotation, making the machine inefficient.
- Brushes: Brushes are components made of carbon or metal, placed in contact with the commutator. Their role is to transfer current between the rotating armature and the external circuit. In motors, they supply current to the armature, and in generators, they collect current from the armature. Though essential for the machine’s operation, brushes wear out over time due to friction and require regular maintenance.
Construction of a DC Machine
The construction of a DC machine involves several critical components that allow it to function efficiently. Here’s a breakdown of its main parts:
- Yoke: The yoke, also known as the frame, is the outer cover of the DC machine. It provides mechanical support for the field windings and poles. It also serves as a protective casing for the inner parts and provides a path for the magnetic flux generated by the field windings.
- Field Windings or Field Coils: These are coils of wire wrapped around poles attached to the yoke. When current flows through these windings, they generate a magnetic field. This magnetic field is necessary for the operation of the machine, as it interacts with the armature to either produce mechanical motion (in a motor) or generate electrical energy (in a generator).
- Armature Windings: The armature windings are conductors placed on the rotor (armature core). These conductors carry the current and interact with the magnetic field to either generate force (in motors) or induce voltage (in generators). The armature windings are usually arranged in slots on the armature core to optimize performance.
- Commutator and Brushes: The commutator and brushes work together to maintain the proper flow of current in the machine. The armature windings connect to the commutator segments, while the brushes allow current to pass between the rotating and stationary parts of the machine.
- Poles: These are magnetic structures attached to the yoke, either carrying the field windings or holding permanent magnets. They create the magnetic field that the armature interacts with to produce torque (in motors) or voltage (in generators).
Equivalent Circuit of DC Machine Armature
To understand the internal behavior of a DC machine, it’s useful to study its equivalent circuit. The equivalent circuit of the armature helps in analyzing the electrical dynamics of the machine.
- Armature Resistance (Ra): This represents the electrical resistance of the armature windings. When current flows through the armature, this resistance causes a voltage drop, reducing the efficiency of the machine. The armature resistance is an important factor in determining the total power losses.
- Armature Inductance (La): The armature windings, being coils of wire, have inductance. This inductance opposes changes in current, which can affect the machine’s dynamic response, particularly during startup or sudden load changes.
- Induced EMF (Ea): The relative motion between the armature windings and the magnetic field generates an electromotive force (EMF) in the armature. In a generator, the induced EMF depends on the speed of rotation and the strength of the magnetic field, while in a motor, it depends on the supply voltage.
- Input Voltage (V): The external electrical supply provides the input voltage to the DC machine in the case of a motor. In the case of a generator, the machine generates the output voltage.
The overall voltage equation for a DC machine’s armature is,
V=Eb+IaRa
Where:
- V is the input voltage of the motor or output voltage of generator,
- Eb is the induced EMF,
- Ia is the armature current, and
- Ra is the armature resistance.
This equation forms the foundation for analyzing the performance of the machine, including the efficiency, torque production, and losses.
The diagram below shows the equivalent circuit of the armature of a DC generator.
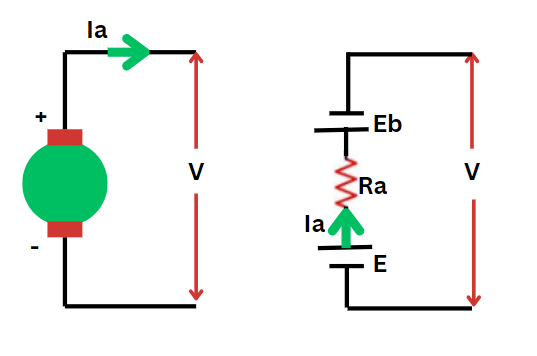
The diagram below shows the equivalent circuit of the armature of a DC motor.
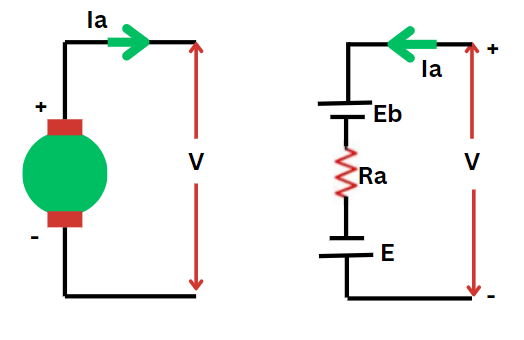
Conclusion
In conclusion, a DC machine is a fundamental device with applications ranging from motors used in transportation and industrial systems to generators that supply DC power. Its versatility, precise speed control, and robust structure make it a key device in electrical engineering. By understanding its structure, types, construction, and the equivalent circuit of the armature, one can effectively harness the potential of DC machines for various technological applications. Whether in a motor or generator configuration, DC machines continue to be relevant, offering controlled performance and reliable operation.
Related Articles: