Learn what a strain insulator is, how it works, and explore its various types and applications in power transmission systems. Understand its role in supporting and insulating overhead lines effectively.
If transmission lines are not properly supported with towers or poles and insulated correctly, electric current may flow to the ground through these structures, posing serious safety risks. To prevent this, transmission lines are always mounted on insulators attached to support poles or towers.
These insulators must have high electrical and mechanical strength, along with a high relative permittivity to ensure effective insulation. Porcelain is the most commonly used material for insulators, though steatite, glass, and composite materials are also used. This article provides an overview of strain insulators.
What is a Strain Insulator?
Definition: A strain insulator is an electrical insulator designed to withstand mechanical strain while electrically isolating conductors. It is primarily used to support and separate transmission lines or radio antennas, especially in high-tension applications. These insulators are placed between two wires or at the end of transmission lines to prevent electrical contact and provide mechanical strength.
Strain insulators are typically used where the conductor’s tension is high, such as at the end poles of overhead lines or at sharp turns. They ensure both mechanical support and electrical insulation, making them essential in maintaining system safety and performance.
Strain insulator diagram is shown below.

Construction of Strain Insulator
Strain insulators are specifically engineered to withstand high mechanical tension while providing effective electrical insulation. Their construction is robust and varies slightly based on the voltage level of the application.
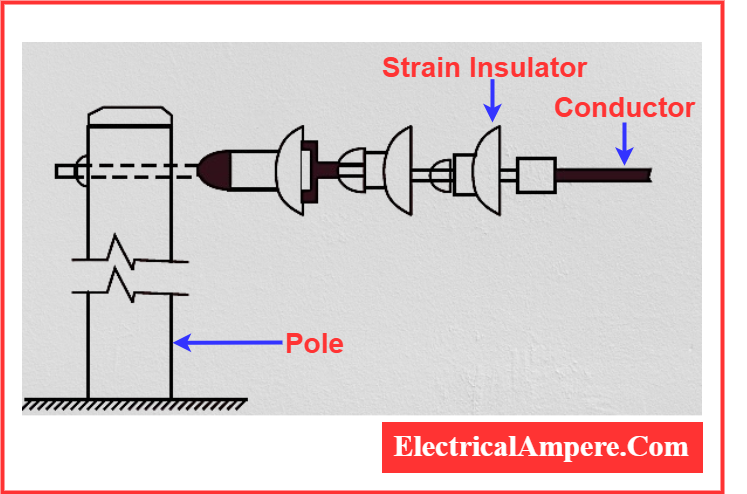
Below are the key components involved in their construction:
1. Insulating Material
The core body of the strain insulator is made from high-dielectric strength materials that resist electrical conduction. Commonly used materials include:
- Porcelain – Highly durable and widely used in traditional applications.
- Toughened Glass – Offers excellent visibility of internal cracks and has self-cleaning properties.
- Polymer Composites – Lightweight and weather-resistant, ideal for modern installations.
These materials ensure reliable insulation between conductors and the supporting structures, even under extreme weather or pollution.
2. Metal Fittings
At both ends of the insulator, metal fittings are securely attached. These fittings serve as mechanical connectors and are typically made from:
- Forged steel
- Galvanized iron
The fittings allow the insulator to be connected to guy wires, tension cables, or line hardware, ensuring both electrical insulation and mechanical strength.
3. Shape and Structure
The shape and design of a strain insulator depend on the voltage level of the system:
- For high-voltage transmission lines, multiple disc-type insulators are connected in series to form a strain insulator string. This structure distributes mechanical load and increases insulation length.
- For low-voltage lines (typically up to 11 kV), a single strain or shackle-type insulator is sufficient. These are often mounted horizontally and have a compact, rugged design.
The structure is optimized to resist environmental stress, mechanical pull, and electrical flashovers.
Working of Strain Insulator
In transmission lines, particularly at corner poles or end points, the conductors experience a high tensile force. To withstand this mechanical strain, strain insulators are used. These insulators are crucial at sharp bends or where the direction of the line changes significantly.
In high-voltage transmission systems, strain insulators typically consist of a string of suspension insulators. These strings are arranged horizontally, with each disc aligned vertically. When the tensile load is very high, multiple suspension strings are connected in parallel using strong steel hardware to evenly distribute the mechanical load.
For low-voltage lines (typically below 11 kV), shackle insulators often serve as strain insulators. These are made from materials like porcelain, glass, or fiberglass, and come with metallic fittings and hardware to connect two cables while keeping them electrically insulated. The compact design helps minimize the spacing between conductors while maintaining safety.
When the line voltage exceeds the insulation capacity of a single insulator unit, multiple insulator discs are connected in series to achieve the necessary insulation level. A steel plate is used to bundle multiple insulator strings when one is not sufficient to handle the strain. One plate is placed at the conductor (live) end, and the other at the tower or pole (support) end.
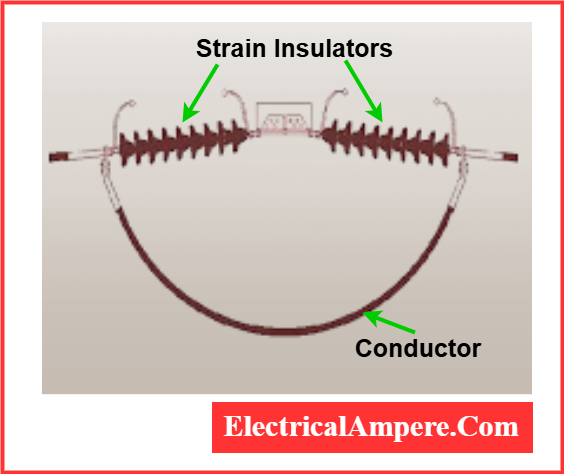
This setup is especially important in long-distance spans such as crossings over rivers, canals, or valleys, where tension forces are significantly higher.
The number of disc insulators used in a string depends on the system voltage:
- For 33 kV systems – 3 disc insulators
- For 66 kV systems – 5 disc insulators
- For 132 kV systems – 9 disc insulators
- For 220 kV systems – 15 disc insulators
These insulators must offer high mechanical strength and excellent electrical insulation to ensure reliable and safe operation of the transmission network.
Types Of Strain Insulator
There are several types of strain insulators, each designed for specific applications based on the mechanical load and electrical voltage requirements. The types of strain insulators generally vary based on their construction and the material used. Here are the main types:
1. Porcelain Strain Insulators:
- Construction: Made of high-strength porcelain, these are the traditional and most common type of strain insulators.
- Application: Used in high-voltage transmission lines where both mechanical strength and electrical insulation are required.
- Advantages: Durable, resistant to weathering, and capable of withstanding high mechanical stress.
- Disadvantages: Heavier than composite insulators and more prone to breakage under impact.
2. Composite Strain Insulators (Polymer Strain Insulators):
- Construction: Made from composite materials such as fiberglass or polymer-based materials with a high mechanical strength core and an insulating outer layer.
- Application: Typically used in areas where weight and impact resistance are important, such as in areas with high wind loads or where transport and handling are challenging.
- Advantages: Lighter than porcelain, more resistant to breaking, and less prone to contamination (dirt and moisture) than porcelain insulators.
- Disadvantages: More expensive than porcelain and can degrade over time under certain environmental conditions (e.g., UV exposure).
3. Cap and Pin Type Strain Insulators:
- Construction: Consists of a “cap” (the upper part that attaches to the line) and a “pin” (the lower part that is attached to the tower or support structure). This type is commonly used for overhead transmission lines.
- Application: Commonly used for low to medium voltage lines or for areas requiring flexibility in installation.
- Advantages: Simple and robust design, easy to install and maintain.
- Disadvantages: Not suitable for very high mechanical loads or extreme environmental conditions.
4. String Insulators:
- Construction: These consist of a series of porcelain or composite insulator discs connected in a series, forming a “string” of insulators.
- Application: Typically used in high-voltage transmission lines where greater mechanical load-bearing capacity and high voltage insulation are needed.
- Advantages: Can handle high mechanical stresses and are more flexible in terms of design.
- Disadvantages: The installation is more complex due to the number of components in the string.
5. Suspension Strain Insulators:
- Construction: These are insulators used in suspension lines that are subjected to less mechanical stress than strain insulators but still need to be durable. They typically have a different mounting configuration.
- Application: Typically used where the conductor is suspended and is subjected to mechanical forces like wind, but not as much as in strain insulators.
- Advantages: Cost-effective for less mechanically demanding applications.
- Disadvantages: Not as durable as strain insulators in high-load situations.
6. Post Type Strain Insulators:
- Construction: A post-type strain insulator is a vertical insulator that attaches directly to the supporting tower, with the conductor hanging from it.
- Application: Commonly used in substation and terminal applications.
- Advantages: Compact design, which is well-suited for certain applications where space is constrained.
- Disadvantages: May not be suitable for extremely high mechanical stress lines.
Each type of strain insulator is selected based on factors like mechanical load, environmental conditions, installation requirements, and cost considerations.
Tests Conducted on Strain Insulators
To ensure the reliability, durability, and safety of strain insulators used in power transmission systems, each insulator must undergo a series of rigorous tests. These tests are classified into three main categories: Type Tests, Performance Tests, and Routine Tests. Each category evaluates different aspects of the insulator’s electrical, mechanical, and physical characteristics.
1. Type Tests
Type tests are conducted to verify the design and ensure the insulator meets standard specifications under typical and extreme conditions. These are generally conducted once for a specific design or type of insulator. The main type tests include:
- Dry Flashover Test:
Measures the voltage at which the insulator flashes over (fails electrically) under dry conditions. - Wet Flashover Test (Thirty-Second Rain Test):
Evaluates the flashover voltage when the insulator is wet due to rain, simulating real environmental conditions. - Impulse Voltage Withstand Test:
Tests the insulator’s ability to withstand high-voltage surges, such as those caused by lightning or switching operations. - Power Frequency Withstand Test:
Checks the insulator’s ability to endure standard power frequency voltage for a specified time without breakdown.
2. Performance Tests
Performance tests assess how the insulator behaves under practical operating conditions. These tests are critical for evaluating long-term durability and operational efficiency. Key performance tests include:
- Temperature Cycle Test:
Subjects the insulator to repeated heating and cooling cycles to check for cracks or other structural changes. - Electromechanical Test:
Combines both electrical and mechanical stresses to determine the insulator’s performance under simultaneous loading. - Puncture Test:
Measures the voltage at which the insulating material breaks down internally. - Mechanical Strength Test:
Verifies the insulator’s ability to withstand the mechanical load applied during service, such as conductor tension. - Porosity Test:
Ensures the material is free from internal pores that could absorb moisture and compromise insulation performance.
3. Routine Tests
Routine tests are performed on every manufactured insulator unit to ensure consistent quality in production. These include:
- High Voltage Test:
Ensures each unit can withstand a specified voltage level without breakdown. - Proof Load Test:
Confirms that the insulator can bear a predefined mechanical load without deformation or failure. - Corrosion Resistance Test:
Checks the resistance of metallic fittings and materials to environmental factors such as moisture, pollution, or chemicals.
These tests are applicable to all types of strain insulators regardless of material or voltage class. By passing these tests, strain insulators are certified as safe and effective for supporting and insulating conductors in overhead transmission lines. Their performance directly impacts the reliability and safety of electrical power systems.
Applications of Strain Insulator
Strain insulators play a critical role in both electrical transmission and structural support. Their primary function is to provide mechanical strength and electrical insulation in locations where conductors are subjected to high tension. Below are the major applications of strain insulators:
1. Overhead Power Transmission Lines
Strain insulators are extensively used in overhead electrical wiring systems to support and insulate conductors. They are especially essential in areas where the line direction changes, such as:
- Dead ends
- River or valley crossings
- Sharp curves or angles in the line
In these situations, conductors are under significant mechanical stress, and strain insulators help maintain both physical integrity and electrical isolation.
2. Radio and Communication Antennas
In addition to power lines, strain insulators are also used to support radio antennas and communication cables, particularly where guy-wires are employed. They electrically isolate the structure while bearing the mechanical load.
3. Outdoor Electrical Installations
Strain insulators are designed to withstand outdoor environmental conditions such as:
- Rainfall
- Humidity
- Pollution in urban or industrial areas
Since outdoor insulators are exposed to contaminants and moisture, their design and shape are critical. For example, if water bridges the gap between conductors, it can form a low-resistance path that leads to electrical leakage or failure.
4. Design Considerations Based on Mounting
Strain insulators are shaped based on how they are mounted:
- Horizontally mounted insulators often have extended flanges to shed water efficiently.
- Vertically mounted insulators are usually bell-shaped, a design that minimizes water accumulation and maintains effective insulation.
5. High-Tension Applications
These insulators are ideal in locations where mechanical strain is very high. They are used to reduce extreme tension on the conductors, preventing damage to the line and ensuring safe and stable operation over long distances.
Advantages of Strain Insulators
Strain insulators offer several functional and safety-related benefits in electrical transmission and structural support systems. Below are the key advantages:
1. Ideal for Low-Voltage Applications
Strain insulators are particularly suitable for low-voltage lines, typically up to 11 kV. They provide sufficient insulation and mechanical strength for these applications while being cost-effective.
2. Effective Ground Isolation
These insulators are used to electrically isolate conductors from the ground, especially in guy or stay wire systems. This prevents unintended current flow to the ground, which enhances the safety and reliability of the system.
3. Durable Construction Using Porcelain
Most strain insulators are constructed from high-grade porcelain, which offers:
- High mechanical strength
- Excellent weather resistance
- Long operational life
Porcelain is also highly resistant to electrical stress, making it ideal for use in outdoor environments.
4. Failsafe Mechanical Support
In the event of an insulator failure or damage, the stay or guy wires remain suspended and do not fall to the ground. This prevents accidents and structural damage by ensuring that mechanical support is maintained even when insulation is compromised.
These advantages make strain insulators a dependable choice for both electrical insulation and mechanical strain handling in overhead power distribution and antenna systems.
Disadvantages of Strain Insulators
While strain insulators offer essential mechanical and electrical benefits, they also come with certain limitations. The key disadvantages are:
1. High Initial Cost
Strain insulators are typically made from high-strength materials such as porcelain, glass, or composite polymers. Their complex structure and the need for durability under mechanical stress make them more expensive than other types of insulators, especially in high-voltage applications.
2. Regular Maintenance Required
In polluted environments, industrial zones, or coastal areas, strain insulators are prone to contamination. This can lead to surface tracking and flashover during wet conditions. As a result, they require:
- Frequent cleaning
- Routine inspections
to maintain reliable insulation performance.
3. Heavy Weight
Strain insulator strings, especially those used for higher voltages, can be physically heavy due to multiple discs and metal hardware. This weight demands:
- Robust support structures
- Strong towers or poles
which can increase the overall structural and installation cost.
Read Next: