Discover the different types of synchronous motors, including non-excited, permanent magnet, and current-excited motors. Learn how each type operates, their advantages, and applications in various industries.
A synchronous motor is an AC motor that operates at a constant speed, which is directly proportional to the supply frequency. Unlike induction motors, synchronous motors maintain a fixed speed regardless of the load, making them ideal for applications requiring precise speed control.
There are two main types of synchronous motors based on excitation methods:
- Non-Excited Synchronous Motors
- Current-Excited Synchronous Motors
Let’s explore these types in detail.
Non-Excited Synchronous Motors
Non-excited synchronous motors do not require external electrical excitation to create the magnetic field. Instead, they rely on the rotor’s material properties and external magnetic influence to achieve synchronization. These motors are further classified into:
1. Hysteresis Motor
Hysteresis motors are single-phase motors with rotors made of ferromagnetic material. A hysteresis motor operates using the principle of hysteresis loss. The rotor, made of ferromagnetic material like chrome-cobalt steel or alnico, aligns with the rotating magnetic field produced by the stator windings.
The stator contains two windings:
- Main winding
- Auxiliary winding
Working Principle:
- When an AC supply is given, the Main winding and Auxiliary winding of the stator generates a rotating magnetic field.
- Eddy currents are induced in the rotor, causing initial movement with a slip.
- As the rotor accelerates, it locks into synchronous speed due to hysteresis torque, eliminating slip.
- These motors are self-starting and operate smoothly with minimal noise.
Applications:
- Precision instruments
- Tape recorders
- Clocks and timers
2. Reluctance Motor
A reluctance motor operates based on the principle that the rotor aligns itself with the stator’s magnetic field to minimize magnetic reluctance. The rotor has salient poles, making it different from standard induction motors. Similar to hysteresis motors, it features main and auxiliary windings that generate a rotating magnetic field. The rotor is designed as a squirrel cage with certain teeth removed to create salient poles. This configuration allows the rotor to align with the stator’s magnetic field, minimizing reluctance.
Working Principle:
- When a single-phase AC supply is applied,, the stator windings create a rotating magnetic field.
- The rotor initially functions like an induction motor, gaining speed due to induced current.
- The rotor attempts to align with the stator’s magnetic field, experiencing reluctance torque. However, due to inertia, it overshoots its position and continues adjusting with each revolution. This process enables the rotor to start rotating.
- At around 75% of synchronous speed, the reluctance torque aligns the rotor with the stator’s magnetic field, achieving synchronism, ensuring that it continues running at a constant speed due to synchronous reluctance torque.
Applications:
- Robotics
- Textile machinery
- Pumps and compressors
3. Permanent Magnet Synchronous Motor (PMSM)
A permanent magnet synchronous motor (PMSM) uses permanent magnets embedded in the rotor to generate a magnetic field. These motors require variable frequency drives (VFD) for starting and speed control.

Working Principle:
- The stator produces a rotating magnetic field when powered.
- The permanent magnets in the rotor create a constant magnetic flux.
- The rotor synchronizes with the stator field at synchronous speed.
- These motors are not self-starting and require electronic controllers.
Applications:
- Electric vehicles (EVs)
- Wind turbines
- HVAC systems
Current-Excited Synchronous Motors
Unlike non-excited synchronous motors, current-excited synchronous motors require an external DC power source to excite the rotor windings, creating a magnetic field. They are also called direct current excited synchronous motors.
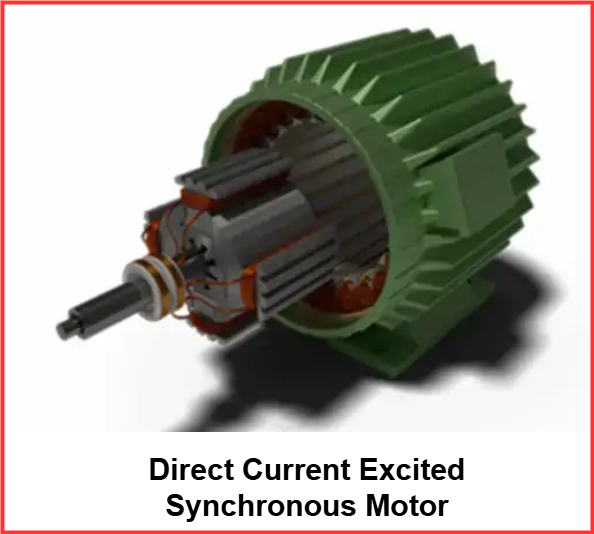
These motors have both stator and rotor windings and can have either cylindrical or salient pole rotors.
Working Principle:
- A separate DC supply energizes the rotor windings.
- The interaction between the stator and rotor magnetic fields produces a constant torque.
- Since they are not self-starting, they utilize damper windings to function as induction motors during startup, allowing them to gradually reach synchronous speed.
Applications:
- Large industrial applications
- Crushers and mills
- Power plants
Conclusion
Synchronous motors are highly efficient AC machines used in precision applications requiring constant speed. Depending on the excitation method, they are classified into non-excited and current-excited synchronous motors.
- Non-excited motors include hysteresis, reluctance, and permanent magnet synchronous motors, ideal for small-scale applications.
- Current-excited synchronous motors require a DC supply for excitation and are used in heavy industrial applications.
Understanding these types of synchronous motors helps in selecting the right motor based on performance needs, efficiency, and application requirements.
Read Next: