Discover regenerative braking in DC motors, a technology that recovers kinetic energy and converts it into electrical power, enhancing efficiency in electric vehicles, trains, and industrial applications.
What is Braking in DC Motor?
Braking in a DC motor refers to the process of reducing or stopping the motor’s speed in a controlled manner. It is essential for ensuring safety, precision, and efficiency in various industrial and automation applications. Proper braking helps protect mechanical components, ensures operator safety, and enhances system performance.
There are several key requirements for motor braking. It is crucial for emergency stops, allowing the motor to halt quickly in critical situations. Controlled speed reduction is necessary for handling descending loads smoothly. Braking also plays a vital role in automation systems that require repeatable positioning and movement accuracy. Additionally, it prevents excessive speed during overhauling conditions, ensuring the motor operates within safe limits.
DC motors use two main types of braking: electrical braking and mechanical braking. Electrical braking methods, such as regenerative braking, dynamic braking, and plugging, use the motor itself to generate braking torque. In contrast, mechanical braking relies on external friction-based braking systems to physically slow down or stop the motor. The choice between electrical and mechanical braking depends on the application, required stopping time, and safety considerations.
What is a Regenerative Braking?
Regenerative braking is a method of braking in which the kinetic energy of the driven load or machinery is converted back into electrical energy and returned to the power supply mains. This process occurs when the load forces the motor to operate at a speed higher than its no-load speed while maintaining a constant excitation.
Under these conditions, the motor’s back electromotive force (Eb) exceeds the supply voltage (V), causing a reversal in the direction of the armature current. As a result, the motor transitions into generator mode, converting mechanical energy into electrical energy and feeding it back into the power source.
Regenerative braking can also function at low speeds if the motor is configured as a separately excited generator. By increasing the excitation as the speed decreases, it ensures that two key electrical equations governing the system remain satisfied.
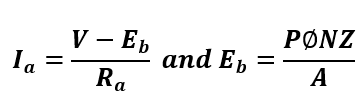
For effective regenerative braking:
- The motor should not enter saturation when excitation increases.
- The generated electrical energy should be efficiently returned to the power supply.
This braking technique is primarily used with shunt and separately excited motors, as they allow for controlled excitation. In compound motors, regenerative braking is feasible only when weak series compounding is used.
Applications of Regenerative Braking
Regenerative braking is widely used in applications that require frequent deceleration and speed control. It is particularly beneficial in systems where a load with high potential energy needs to be maintained at a constant speed while descending.
Key applications include:
- Electric Locomotives – Regenerative braking helps in energy-efficient braking of trains, reducing energy consumption by feeding power back into the grid.
- Elevators – Used to control the descent of elevators by converting kinetic energy into electrical energy, improving efficiency.
- Cranes and Hoists – Helps regulate the speed of lifting and lowering heavy loads, preventing excessive wear on mechanical braking systems.
- Electric Vehicles (EVs) and Hybrid Vehicles – Enhances battery life and efficiency by recovering energy during braking.
- Industrial Drives – Applied in conveyor systems and rolling mills to manage motor speeds and optimize power usage.
Limitations
Regenerative braking is not suitable for stopping a motor completely. Instead, it is used to regulate speed above the no-load speed of a motor. For regeneration to occur, the back EMF (Eb) must be greater than the supply voltage (V), reversing the armature current and shifting the motor’s operation from motoring to generating mode.
Regenerative Braking in DC Motor Formula
The formula for regenerative braking in a DC motor is derived from the armature voltage equation:
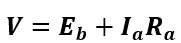
where:
- V = Supply voltage (V)
- Eb = Back EMF (V)
- Ia = Armature current (A)
- Ra = Armature resistance (Ω)
During regenerative braking, the motor speed increases due to an external force (such as a descending load), causing the back EMF Eb to exceed the supply voltage V. This reverses the armature current:
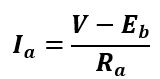
For regeneration to occur:
Eb>V
This reversal of armature current allows the DC motor to function as a generator, sending power back to the supply system.
Regenerative Braking in DC Shunt Motors
In normal operation, the armature current (Ia) in a DC shunt motor is determined by the following equation:
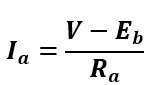
where:
- V is the supply voltage,
- Eb is the back EMF,
- Ra is the armature resistance.
During regenerative braking, if the motor is driving a descending load, such as in cranes, hoists, or lifts, the motor speed increases beyond its no-load speed. This causes the back EMF (Eb) to exceed the supply voltage (V), leading to a reversal of armature current (Ia).
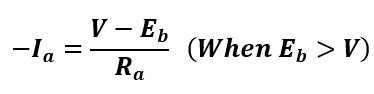
At this point, the motor starts functioning as a generator, converting mechanical energy from the moving load into electrical energy, which is fed back into the supply system. This process enhances energy efficiency and helps control the speed of the motor without excessive wear on mechanical brakes.
Regenerative Braking in DC Series Motors
In a DC series motor, an increase in speed results in a decrease in both armature current and field flux. Unlike shunt motors, the back EMF (Eb) in a series motor cannot exceed the supply voltage because the field current is directly dependent on the armature current. This makes traditional regenerative braking challenging in DC series motors.
However, regeneration is still possible and is widely used in applications where DC series motors are essential, such as in traction systems, elevator hoists, and electric locomotives. For instance, in an electric locomotive descending a gradient, regenerative braking helps maintain a constant speed. Similarly, in hoist drives, it prevents excessive acceleration when lowering a heavy load.
One commonly used method of regenerative braking in DC series motors is modifying the motor connection to behave like a shunt motor. Since the field winding has low resistance, a series resistor is added to limit the current to a safe value. This adjustment allows the motor to function as a generator and return energy to the supply system efficiently.
Advantages and Disadvantages of Regenerative Braking
Advantages:
- Energy Recovery: Regenerative braking converts the kinetic energy of the motor into electrical energy, which can be fed back into the power system for reuse, reducing overall energy consumption.
- Improved Efficiency: It enhances the efficiency of electrical systems, especially in applications where energy savings are a priority, such as electric vehicles and industrial drives.
- Smooth Deceleration: This braking method provides controlled and smooth deceleration, preventing sudden stops and ensuring a seamless transition in speed reduction.
Disadvantages:
- High Implementation Cost: The complexity of regenerative braking systems makes them more expensive to install and maintain compared to conventional braking methods.
- Requires Specialized Equipment: Not all applications can support regenerative braking, as it requires a compatible power supply system capable of handling and storing the returned energy efficiently.
Read Next: