In electrical engineering, safety and reliability are very important. One key component that ensures both is the High Rupturing Capacity (HRC) fuse. Electricity plays a vital role in our daily lives, from homes to industries. To protect people and equipment, electrical systems need strong circuit protection devices. One such important device is the HRC fuse. HRC stands for High Rupturing Capacity, and this fuse is designed to safely break high fault currents. Because of this, it is widely used in industrial applications.
This article explains HRC fuses in detail, covering their construction, working, types, and applications. Knowing about HRC fuses is essential for anyone involved in electrical system design, maintenance, or operation.
What is HRC Fuse?
An HRC fuse, or High Rupturing Capacity fuse, is designed to handle high fault currents safely. It prevents explosions and protects nearby equipment from damage. HRC fuses are widely used because they break the circuit when the current exceeds a set limit. This helps protect electrical circuits from faults. The Full Form of HRC Fuse- High Rupturing Capacity Fuse.
An HRC fuse has a high rupturing capacity. This means it can safely interrupt fault currents much higher than the circuit’s rated current. Under normal conditions, the fuse allows current to flow smoothly through its element. However, during a fault, it must quickly isolate the faulty circuit to prevent damage. Unlike conventional fuses with lower breaking capacities, an HRC fuse can handle heavy overloads or short-circuit faults of up to 1500A or more, regardless of its amp rating. This is possible due to its advanced construction, which includes heat-resistant materials for better performance.
Simply put, an HRC fuse is a specially designed, high-performance circuit protection device. It can handle fault currents much higher than its normal rated current, ensuring the electrical system stays safe from surges, spikes, and accidents. Because of its high breaking capacity, HRC fuses are widely used in industrial power distribution and equipment protection, where large fault currents must be quickly interrupted.
What is the Use of HRC Fuse?
An HRC fuse is crucial in protecting electrical equipment from overcurrents, which can lead to overheating and damage. These fuses are widely used in industrial and residential settings, as they help prevent electrical fires and equipment failures. An HRC fuse (High Rupturing Capacity fuse) is designed to handle short-circuit currents for a specific period. When a fault occurs, the fuse wire inside melts and breaks the circuit, stopping the flow of electricity. Typically, HRC fuses are made from glass or other chemical compounds, ensuring durability and efficient operation.
Construction of HRC Fuse
HRC fuses are designed with a special construction that enables them to interrupt heavy overcurrents effectively. The body of an HRC fuse is made from a highly heat-resistant material, usually ceramic, which ensures durability and safety. Inside the fuse, metal end caps are firmly welded to a silver current-carrying element, allowing efficient conductivity and reliable operation.
Fuse Construction
The inside of the fuse body is filled with powder materials like quartz, plaster of Paris, marble dust, or chalk, which prevent overheating when current flows through the fuse. When a fault occurs, the heat generated melts the fuse element, turning it into silver vapor. At the same time, this vapor reacts with the filling powder, creating a high-resistance material. As a result, this reaction significantly reduces arc formation, ensuring that the fuse safely interrupts the fault current and protects the electrical system. The HRC fuse diagram is shown in the below image.
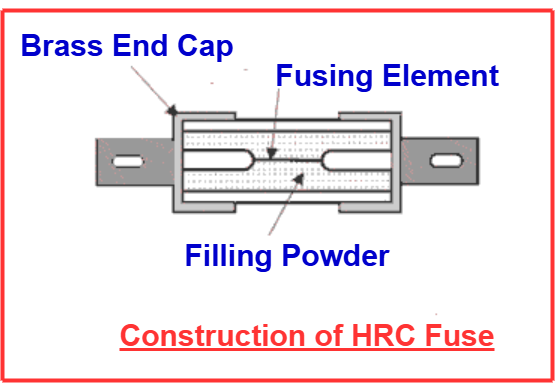
Typically, copper or silver is used as the fuse element because of their low specific resistance, allowing efficient current flow. Moreover, the fuse element usually consists of two or more sections connected through tin joints. Since tin has a melting point of 240°C, which is much lower than silver’s melting point of 980°C, the tin joints melt first. As a result, this prevents the fuse from overheating during short circuits and overloads, ensuring a safe and controlled interruption of excessive current flow.
The key design features of an HRC fuse are as follows:
- Heat-resistant outer body: Made of materials like ceramic or fiberglass to withstand high temperatures without breaking down.
- Internal filler: The inside of the fuse is filled with powders like silica sand, quartz, or chalk to absorb heat during faults.
- Silver fuse element: The element is shaped to melt at a specific temperature when there is an overload.
- Sealed end caps: Metal caps are sealed to keep the fuse airtight, preventing arc quenching and energy loss.
- Sealant: Additional sealants like epoxy resin are used to strengthen joints and protect against moisture, oxidation, and pressure.
- Insulating covers: Some fuses have polymer casings or insulation sleeves for extra safety.
The strong, sealed housing and precise internal design allow HRC fuses to handle heavy overloads. This prevents damage to the outer body and protects the system.
Working Principle of HRC Fuse
The working principle of an HRC fuse is simple:
- Under normal conditions, the silver element allows the current to flow smoothly, and heat is dissipated, keeping the element intact.
- During an overload or fault, the current exceeds the rated limits, causing the silver element to overheat.
- The element begins to melt at weak points due to concentrated heat.
- As the melting progresses, the circuit is broken because the molten silver disconnects the end caps.
- The inner filler material and electrode seal absorbs the heat generated, limiting the temperature rise.
- Any arc that forms is quickly quenched by a chemical reaction between the silica filler and silver vapor, preventing further damage.
- The sealed, insulated body helps prevent energy loss and controls the temperature to safely interrupt heavy overcurrents.
- After the fault is cleared, the melted element must be replaced before power is restored.
- The controlled melting of the element with the specialized construction, allows HRC fuses to interrupt heavy currents safely.
Materials Used for Fuse Wires
Fuse wires in HRC fuses are made from:
- Silver: This is preferred for its high conductivity and predictable melting properties.
- Copper: Commonly used for lower-cost applications, providing good conductivity and performance.
Key Terminologies of HRC Fuse
It’s important to understand key terms to grasp how HRC fuses work:
- Rated Current: The maximum current the fuse can carry without blowing.
- Breaking Capacity: The maximum fault current the fuse can safely interrupt.
- Rated Voltage: The maximum voltage the fuse can handle.
- Pre-Arcing Time: The time taken for the fuse to interrupt the circuit after the overcurrent condition starts.
- Rupturing Capacity: The highest fault current a fuse can safely interrupt, generally 1500A or higher for HRC fuses.
- Fuse Rating: Specifies the current and voltage limits the fuse can reliably protect in its application.
- Fusing Factor: The ratio between the element’s rated current and its melting or breaking points under standard temperature conditions.
- Fuse Speed: The time taken by the fuse to open under fault conditions, classified as very fast, fast, medium, or slow.
- Load End and Line End: Connector terminals of a fuse—the line end connects to the live supply, and the load end connects to the load/circuit.
It is important to understand these terms related to ratings, performance, and connections when working with HRC fuses.
HRC Fuse Element
The fuse element is crucial in determining the electrical and technical properties of an HRC fuse. Common materials used for fuse elements include:
- Silver: The most popular choice due to its excellent conductivity, consistent melting, and ability to quench arcs during overload. Its fusing factor is around 5-6.
- Copper: Less common than silver, but still a good conductor, especially at lower thicknesses. Its fusing factor is about 15.
- Aluminum: Lightweight with decent conductivity, but its high fusing factor of around 30 requires a larger cross-section to match the rating of silver or copper.
The shape, size, quantity, and special coatings or treatments applied to the fuse element affect its performance. Examples of element types include mono-filament, ribbon, or multi-filament. For higher ratings, the elements are made of multiple silver strips that are brazed or welded together.
Coatings like nickel, tin, or gold improve contact resistance and stop oxidation. Powder coating makes the element melt uniformly. Profiling cuts grooves in the element to concentrate heat during a fault, ensuring focused disconnection. The careful design of the fuse element with other features adjusts the time-current and current-limiting characteristics. Thus, the HRC fuse provides effective circuit protection for industrial needs.
Types of HRC Fuse
There is no one-size-fits-all design for HRC fuses. The design depends on factors like voltage class, installation method, intended use, and international standards. As a result, HRC fuses come in various configurations.
Low Voltage HRC Fuses
Low Voltage HRC fuses keep electrical systems safe and reliable. They are used in systems with voltages below 1000V. These fuses can interrupt high fault currents without damaging equipment or the surrounding area.
Fuse Body: The fuse body of low-voltage HRC fuses is made from heat-resistant materials like ceramic or fiberglass. These materials ensure durability and help the fuse handle high temperatures during faults.
Metal End Caps: The fuse body has metal end caps at both ends, securely welded to the fusible element. These caps help with easy installation and ensure a reliable electrical connection.
Fusible Element: The fusible element, usually made of silver or copper, is the key part that interrupts the circuit during overcurrent conditions. Its precise design ensures it melts correctly during faults.
Filling Material: The fuse body is filled with granular materials like quartz, plaster of Paris, marble dust, or chalk. This material absorbs heat generated by the melting fusible element and helps extinguish the arc when the fuse operates.
- Applications: Low voltage HRC fuses are used in residential and commercial electrical installations to protect circuits from overcurrent situations.
- Characteristics: These fuses are rated for voltages up to 1000V and typically have breaking capacities of up to 100kA, ensuring effective protection against high fault currents.
High Voltage HRC Fuses
High Voltage HRC fuses are designed to safely interrupt fault currents in electrical systems that operate at high voltage levels, protecting both the equipment and infrastructure.
Fuse Body: The fuse body is made from durable, heat-resistant materials like ceramic or fiberglass, enabling it to endure the high temperatures and stresses that come with high-voltage faults.
Metal End Caps: The fuse body features metal end caps welded to the fusible element. These caps ensure secure electrical connections and make installation and replacement straightforward.
Fusible Element: The fusible element is typically made from silver or copper, chosen for its high conductivity and reliable melting properties under overcurrent conditions.
Filling Material: Inside the fuse body, materials like quartz or silica sand are used to absorb heat and extinguish the arc formed when the fusible element melts. This ensures safe and effective current interruption during fault conditions.
- Applications: High Voltage HRC fuses are primarily used in industrial and utility sectors to protect critical electrical systems.
- Characteristics: These fuses are rated for voltages above 1000V and are specifically designed to manage very high fault currents, ensuring reliable protection of equipment and infrastructure.
Cartridge Type HRC Fuses
These fuses have a straight, metal cylindrical shape and are typically available in sizes like 10x38mm and 14x51mm. They can be screwed into panels or holders from either end and are rated up to 15kV.
- Applications: Commonly used in electronic and electrical devices for circuit protection.
- Characteristics: They have a compact, cylindrical design and are easy to replace, making them a popular choice for various applications.
Blade Type HRC Fuses
Blade-type HRC fuses are generally used for control circuit protection. They come with solder, quick connect, or crimp-type terminations and are housed in ceramic material. They are typically rated from 12V to 230V.
- Applications: Commonly used in automotive and industrial applications for circuit protection.
- Characteristics: They feature flat, blade-like terminals that allow for quick installation and removal, making them efficient and convenient to use.
Characteristics of HRC Fuse
Besides their high rupturing capacity, HRC fuses have several other important characteristics:
- Voltage Ratings: These fuses are available in a wide range, starting from 220V and extending to over 40kV, depending on the application. They follow international ratings from utilization voltage up to the maximum system voltage.
- Current Ratings: HRC fuses can handle currents from less than one amp to several hundred amps, based on the equipment’s Full Load Amp (FLA) or Overcurrent Protective Device (OCPD) size.
- Breaking/Fusing Capacity: HRC fuses are generally rated for breaking capacities of 1500A or higher, regardless of their current rating. This high breaking capacity ensures proper coordination with downstream protection devices.
- Interrupting Time: The interrupting time varies based on the fuse type. For semiconductor fuses, it can be less than 1 second, while for thermally tolerant motor starters, it can be several seconds.
Advantages of HRC Fuse
Here are some key advantages of HRC fuses:
- Safety: They prevent damage to electrical systems and reduce the risk of fires.
- Reliability: HRC fuses provide consistent protection against overcurrents.
- Ease of Replacement: Once blown, they are simple to replace.
- Fault Current Handling: They can clear both high and low fault currents.
- Durability: They do not deteriorate with age, ensuring long-lasting performance.
- High-Speed Operation: HRC fuses operate quickly to interrupt current in fault conditions.
- Maintenance-Free: They require no maintenance during their service life.
- Cost-Effective: They are cheaper than other circuit interrupting devices with similar breaking capacity.
- Consistent Performance: HRC fuses maintain consistent and reliable performance throughout their lifespan.
Disadvantages of HRC Fuse
Here are some considerations when using HRC fuses:
- Initial Cost: They have a higher initial cost compared to standard fuses.
- Replacement Needed: After operation, HRC fuses must be replaced, unlike resettable circuit
Applications of HRC Fuse
HRC fuses are used in several sectors:
- Residential Use: HRC fuses to ensure safety in home electrical circuits.
- Industrial Machinery: They protect heavy machinery from overcurrent damage.
- Power Distribution: These fuses safeguard transformers and feeders in substations and distribution networks.
- Automotive Industry: They protect vehicle electrical systems from overcurrents.
Conclusion
HRC fuses play a key role in protecting electrical systems from overcurrent conditions. Their ability to handle high fault currents with their reliable performance and safety features, makes them essential in various applications.
Related Artciles: