Learn how to connect a 3-phase motor in star and delta configurations. Step-by-step guide with diagrams to ensure proper wiring and efficient motor operation.
A 3-phase induction motor can be connected in either a star or delta configuration, depending on the supply voltage. The motor has three windings for each phase for a single voltage rating and six windings for a dual voltage rating motor. The internal construction and coil connections within the motor are specified during the manufacturing process.
Three-phase motors can be connected in two types of configurations:
- Star &
- Delta
In the high-voltage configuration, the two windings of each phase are connected in series. This arrangement ensures that the maximum supply voltage is evenly distributed across the windings and each winding carries the nominal current.
In the low-voltage configuration, the two windings of each phase are connected in parallel, resulting in lower supply voltage distribution across the windings, and the nominal current flows through each winding.
It is important to note that the low-voltage connection requires twice the current from the source compared to the high-voltage connection. Most motors display two sets of voltage and current values on their nameplates.
Three independent windings are securely held inside the motor’s stator slots. These windings are electrically spaced 120 degrees apart. The motor operates on a three-phase alternating current (AC) system.
A star connection has four wires, while a delta connection has three wires.
A method of starting mechanism for a three-phase alternating current induction motor is the star-delta connection. A starter is typically used to start a motor smoothly. The motor is started by reducing the starting current with a star-delta starter.
The star-delta connection is a common method for starting a three-phase alternating current induction motor. A star-delta starter is used to ensure a smooth start by reducing the motor’s starting current.
What is a Three-Phase Motor?
A three-phase motor is an electric motor powered by three separate phases of electrical power. It operates on alternating current (AC) and requires a three-phase electrical supply to function.
Any three-phase winding circuit can be connected in a star or delta configuration. The star connection connects all of the coil’s ends to a coon point and is powered by the other free ends.
Any three-phase winding circuit can be connected in a star or delta connection. In a star-connection, all the coil ends are joined at a common point, while the remaining free ends are connected to the power supply.
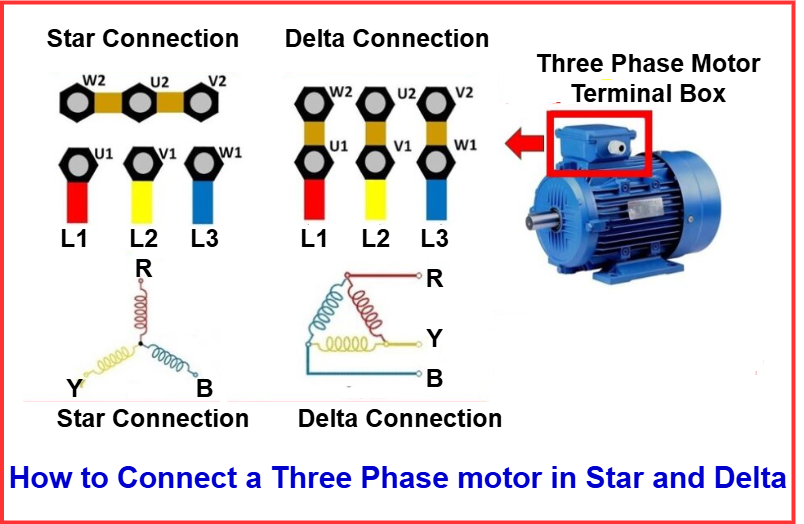
In a delta connection, each end of a coil is connected to the start of the next phase, forming a closed loop and enabling the system to transfer power through the connection points.
The current flowing through each phase coincides with the line current in the star connection, while the voltage supplied to each phase is (1/√3) less than the line voltage.
In a star connection, the current flowing through each phase is equal to the line current, while the voltage across each phase is (1/√3) of the line voltage.
In a delta connection, the current through each phase is (1/√3) of the line current, while the voltage across each phase is equal to the line voltage.
his section will cover the configuration of both Star and Delta connections and the procedure for connecting a 3-phase motor in each configuration.
Asynchronous 3 Phase Motor
Asynchronous 3-phase motors are classified into two types.
- The first category includes motors with wound rotors.
- The second category is the motors with a shorted rotor, commonly known as a squirrel cage rotor, due to its cage-like structure.
Advantages of 3-phase motor over Single-Phase Motors
Efficiency and Power: Higher power output than single-phase motors, reduced vibration, and smoother operation due to a consistent power supply.
Stability and Balance: Enhanced Stability due to evenly distributing power across the three phases, resulting in reduced electrical system stress due to balanced loads.
Acceptability of High Loads: Ideal for heavy-duty industrial applications due to its reliable power source and ability to handle large torque loads efficiently.
Typical Applications of Three-Phase Motor
- They are used in pumps, conveyor belts, compressors, and other heavy machinery.
- Crucial for production lines in factories and industrial plants.
- They are used in HVAC systems, elevators, and large-scale air conditioning units.
- Widely used in commercial buildings for its reliability and efficiency.
- Grain handling equipment, irrigation systems, and agricultural machinery are all powered by three-phase electric power.
- Their strength and power make them essential for a wide range of farming operations.
- They are used for propulsion systems in trains, ships, and certain types of vehicles.
- They are used for power delivery for transportation machines.
- Motors are used in wind turbines and hydropower generators which are used to produce electricity.
- Their reliability and power output make them ideal for use in renewable energy systems.
Star-Delta Motor Connection
An electric motor’s stator has three windings, each with two terminals. The first winding has endpoints U1 and U2, the second winding has endpoints V1 and V2, and the third winding has endpoints W1 and W2.
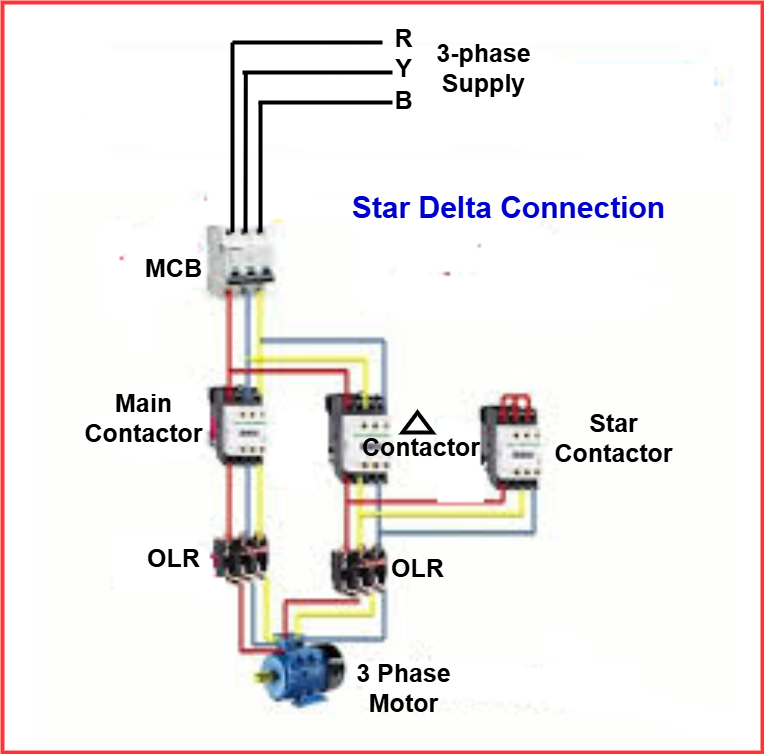
What is a Star Connection?
A star connection, also known as a Y connection, is formed by connecting the three terminals of a three-phase motor in a configuration that resembles the shape of the letter “Y.”
In a star connection, the core of the “Y” is created by joining the three motor terminals (U, V, and W) at a single common point.
Step-by-Step Procedure for Star Connection
Motor Terminal Identification (U, V, W)
To create a star connection, connect the winding ends W2, U2, and V2, as shown in the diagram below, corresponding to the terminals of an electric motor.
Terminal Connections for Star Arrangement
The three-phase power supply lines L1, L2, and L3 are connected to the winding terminals U1, V1, and W1, respectively, as shown.
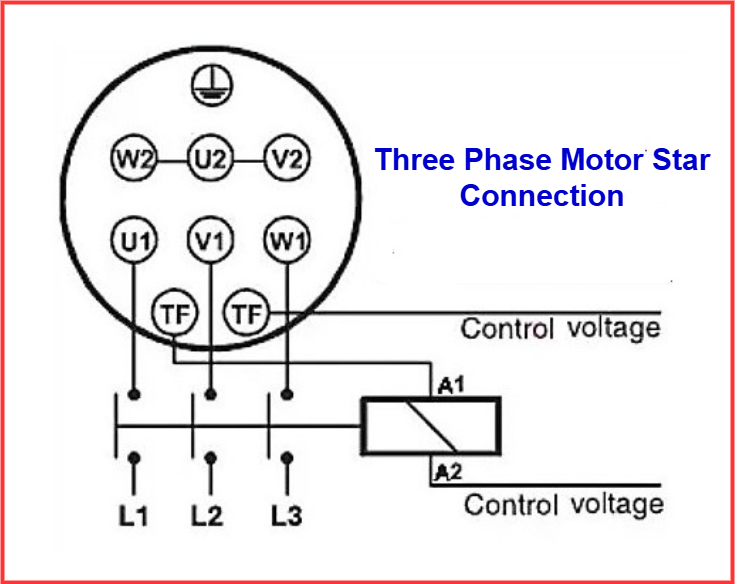
Consider the following key points in a balanced star-connected network:
- Line voltages are √3 times the phase voltages.
- Line currents are equal to phase currents.
- Line voltages are separated by 120 electrical degrees.
- Line voltages lead their respective phase voltages by 30 degrees.
Advantages of Star Connection
- Ensures a balanced voltage supply to the motor windings, reduces stress, and improves motor performance.
Applications of Star Connection
- Perfect for applications needing a smooth start or handling varying loads.
- Commonly used in motors driving blowers, fans, pumps, and other machinery requiring a steady and efficient operation.
Safety Measures in a Star Connection
- Ensure the motor is disconnected from the power source before making any connections.
- Double-check the connections against the motor’s markings or instructions to avoid wiring errors.
- If the wiring is complex or uncertain, consider consulting a certified technician or electrician.
What is a Delta Connection?
A delta connection, symbolized by the Greek letter Δ, connects the three terminals of a three-phase motor in a triangular configuration.
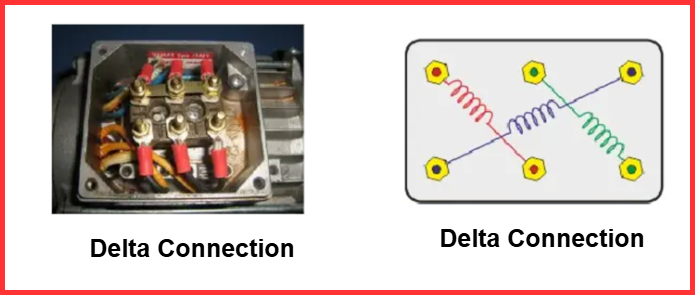
Step-by-Step Procedure for Delta Connection
Motor Terminal Identification (U, V, W)
In a motor with a delta connection, the U, V, and W terminals are interconnected with their adjacent terminals, forming a closed loop shaped like the Greek letter Δ.
Terminal Connections for Delta Arrangement
To create a delta connection, connect the end of coil U1 to the end of coil W2, coil V1 to U2, and coil W1 to V2. The diagram below shows the delta connection configuration in an electric motor.
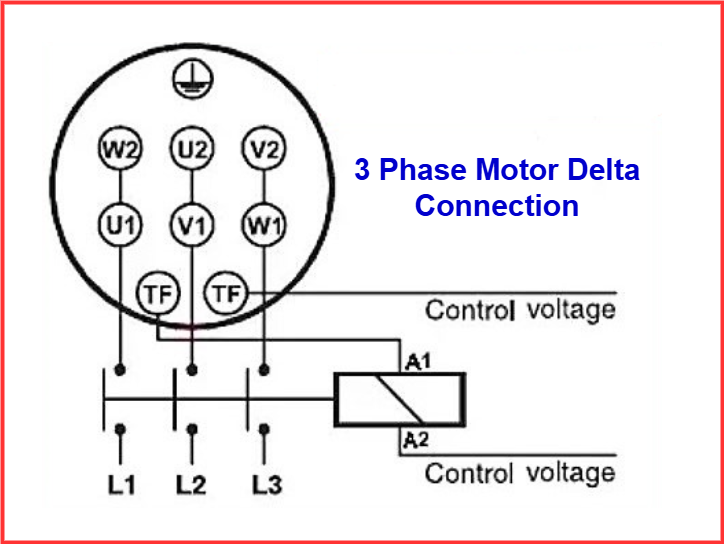
Electric motors are generally connected in a star or delta configuration based on the input voltage. However, starting the motor in a star-delta configuration is also possible, provided the motor’s delta voltage rating matches the supply voltage.
In a delta connection, the opposite ends of the three-phase windings are interconnected.
Because only one phase is included between any pair of line outers in delta, the potential difference between the line outers is referred to as the line voltage and is equal to the phase voltage.
In a delta connection, each pair of line terminals includes only one phase. As a result, the potential difference between the line terminals, known as the line voltage, is equal to the phase voltage.
VL=VP
Where,
VL = Line Voltage
VP = Phase Voltage
The following key points are important regarding the delta connection system.
- Line voltage equals phase voltage.
- Line currents lag phase currents by 30 degrees.
- Line currents are spaced 120 degrees apart.
- Line currents are √3 times the phase currents.
Advantages of a Delta Connection
- This type of connection is better suited for applications requiring rapid acceleration, as it provides higher starting torque compared to star connections.
- Additionally, its wiring configuration uses less copper resulting in cost savings.
Applications of a Delta Connection
- It is used in motors designed for high-torque applications, such as elevators, conveyors, and machinery requiring high starting torque.
Safety Measures of a Delta Connection
- Ensure the motor is disconnected from the power source before doing wiring.
- Cross-check the wiring with the motor’s manual to verify correct connections.
- If you’re unsure about the wiring connections, it’s recommended to consult a qualified electrician or technician.
What are the differences between Star & Delta connections?
Star Vs Delta Connections
Category | Star Connection | Delta Connection |
Voltage | The phase voltage is lower in comparison to the delta connection. | The phase voltage is higher compared to a star connection. |
Current | Due to the lower phase voltage, the line current is higher than in the delta connection. | The line current is lower compared to a star connection. |
Torque | Compared to the delta connection, it provides a lower starting torque. | In comparison to a star connection, it provides higher starting torque. |
Torque Application | It is ideal for applications that demand constant torque and moderate starting torque. | It is ideal for applications that require high starting torque, rapid acceleration, or handling heavy loads. |
Efficiency | Offers efficiency and stability in situations that require moderate starting torque. | It is more efficient in applications that require high starting torque, but continuous operation at high torque may lead to motor stress. |
Performance | Used in situations where the motor windings require a balanced voltage supply. | It is ideal for conditions requiring quick acceleration or managing heavy loads. |
When should utilize Star and Delta?
- The star connection is used for applications requiring more current and a neutral point, while the delta connection is preferred for high-voltage applications.
- Generally, the star connection with a neutral is utilized for distribution, and the delta connection is employed for transmission
What happens if a delta-connected motor is connected to a star connection?
Since line voltage is √3 times the phase voltage and line and phase currents are equal, a star connection is generally used for higher voltage and lower current ratings. Conversely, with line and phase voltages being equal, and line current being √3 times the phase current, the delta connection is used for lower voltage and higher current ratings. These statements assume a balanced three-phase power supply and equal power output for star and delta connections.
Reconnecting a delta-connected three-phase induction motor as a star results in a phase voltage of 1/√3, approximately 58% of its original value. Since torque is proportional to the square of the voltage, it will be reduced to 1/3, or approximately 33.33% of its previous value. In such cases, the higher torque requirement may cause the motor to stall.
Also, the line current will be √3 or 1.732 times higher, resulting in higher line loss and, in certain situations, insulation failure. Because the load’s power is the same as the torque, the speed becomes three times the rated value, which may cause severe damage to the load. Over-speeding may cause rotor damage.
Additionally, the line current will be √3 (or 1.732) times higher, leading to increased line loss and heat and, in some cases, insulation failure.
Therefore, under normal operating conditions, the star or delta connection should not be altered.
Which of the three-phase connections, star or delta, has the greater power handling capacity?
Most motors are designed to operate continuously in a delta connection, where they deliver rated power. During startup, they are initially connected in a star configuration to reduce the starting current. As the motor approaches its rated speed, the connection is switched to delta, as it delivers the rated power delivery capacity.
Motors with lower power ratings are specifically designed to operate in a star connection, as they only feature three connections.
Why is there no neutral wire in a delta connection?
In a balanced system, where all currents and power factors are equal, the phasor sum of all line currents equals 0A. As a result, there is no need for a neutral wire in a balanced system.
What is the formula for a three-phase motor’s star connection?
Three-phase power, voltage, and current values for the Star Connection (Y) are as follows:
VL = √3 VPH (or) VL = √3 EPH
Line voltages (VL) are 30° ahead of their corresponding phase voltages.
How to choose between a Star and a Delta Motor Connection?
The motor is connected in delta to deliver full power at rated speed. However, it draws a large current during startup. To limit the high starting current, the motor is initially connected to the star and then switched to delta using a star-delta starter. For light loads, the motor can be switched from delta to star connection.
Why are Star and Delta Connections used in three-phase circuits?
Star and Delta connections offer distinct advantages. Star connections typically include a neutral point, allowing for easier measurement of line and phase currents. On the other hand, delta connections provide higher voltage tolerance compared to star connections. Additionally, a particular wiring method known as zigzag wiring combines the benefits of both star and delta connections.
What makes Star Connection preferable to Delta?
Star connections are commonly used in power transmission networks for longer distances, while Delta connections are primarily employed in distribution networks for shorter distances. In a Star connection, each winding receives 230 volts, whereas in a Delta connection, each winding receives 415 volts.
Application of the Star and Delta Connection
- A star connection is generally used when a neutral point and two separate voltages are needed, such as in a distribution system.
- Delta connections are commonly preferred when a neutral conductor is not needed, such as for transmitting high-voltage power. Additionally, delta connections are recommended for managing 3rd harmonics.
- In three-phase systems, star and delta connections are widely used.
- Three-phase transformers are generally connected in various combinations of star and delta configurations.
- Star-star connection is used in the autotransformer.
- Delta-delta connected transformers are generally used for high-voltage transmission.
- In most cases, a delta-star-connected transformer is used as a distribution transformer.
Codes and Standards
- IEC 60034-1 (Rotating Electrical Machines – Part 1: Rating and Performance)
- IEC 60204-1 (Safety of Machinery – Electrical Equipment of Machines – Part 1: General Requirements)
- NFPA 70 (National Electrical Code – NEC)
- IS 325 (Three-Phase Induction Motors – Specification)
- IEC 60947-4-1 (Low-voltage Switchgear and Controlgear – Part 4-1: Contactors and Motor-Starters)
Summary
A three-phase system can be connected in two configurations: Star or Delta.
In a star connection, the line-to-line current is equal to the line-to-neutral current. However, the voltage between lines is equal to the square root of three times the voltage between lines and neutral.
In a delta connection, the voltage across each element is equal to the line voltage. However, the current flowing through each element is tripled compared to the line current.
Both connections deliver an equal amount of power.
Read Next: