Learn about braking in electrical systems and explore the types of braking—Regenerative, Plugging, and Dynamic Braking. Understand how each method works to control motor speed, improve efficiency, and enhance safety in industrial and automotive applications
The term braking originates from the word brake, which refers to a device used to slow down or stop moving or rotating equipment, such as vehicles and locomotives. Braking is the process of applying a brake to reduce the speed of a machine.
Braking can be broadly classified into two types:
- Mechanical Braking
- Electrical Braking
Since our focus is on electrical engineering, we will discuss electrical braking rather than mechanical braking. In mechanical braking, speed reduction is achieved through friction-based mechanical components. However, electrical braking is more advanced and relies on controlling flux and torque direction within the motor.
The fundamental concept behind all types of electrical braking is the reversal of flux direction to oppose the motion and slow down the machine. This principle is widely used in industrial motors, locomotives, and electric vehicles, making braking an essential aspect of modern electrical systems.
In conclusion, braking is the process of slowing down a rotating machine, and both mechanical and electrical braking play a crucial role in various industries.
Types of Braking
Braking is essential for reducing or stopping the speed of electric motors. Since different types of motors exist—such as DC motors, induction motors, synchronous motors, and single-phase motors—their braking methods also vary. However, braking techniques can be categorized into three main types, applicable to most motors:
- Regenerative Braking
- Plugging Braking
- Dynamic Braking
1. Regenerative Braking
Regenerative braking occurs when the motor’s speed exceeds the synchronous speed, causing it to act as a generator. In this process, the load supplies power back to the system. This happens when the rotor spins faster than the synchronous speed, reversing the current flow and the direction of torque, which slows the motor down.
While regenerative braking is efficient and energy-saving, its main drawback is the mechanical and electrical stress that high-speed operation can cause. However, with the use of a variable frequency drive (VFD), regenerative braking can also be implemented at lower speeds for better control.
Regenerative braking offers several advantages, with the most significant being reduced power consumption. By converting kinetic energy back into electrical energy, it enhances overall system efficiency, making it an energy-saving alternative to traditional braking methods.
However, regenerative braking also has some disadvantages. A major drawback is that if the motor exceeds the synchronous speed, it can lead to mechanical and electrical damage. This limits its application, as regenerative braking can only occur at a sub-synchronous speed when a variable frequency source is used.
Regenerative braking is particularly useful in applications where frequent braking and controlled slowing of vehicles are required. It is especially effective in maintaining a constant speed when handling descending loads with high potential energy.
This braking technique is commonly used in systems that require controlled speed regulation, such as electric locomotives, elevators, cranes, and hoists. However, it is important to note that regenerative braking is not designed to completely stop a motor but rather to regulate its speed above the no-load speed.
2. Plugging Type Braking

Plugging Braking, also known as reverse current braking, is a braking method where the supply terminals of the motor are reversed to generate a counter torque that opposes the motor’s normal rotation. This effectively slows down the motor by forcing it to operate in the opposite direction, providing a rapid braking effect.
When the supply polarity is reversed, the rotational torque and electromagnetic force (EMF) oppose each other, generating a strong braking torque that quickly reduces the motor speed. To prevent excessive current from flowing through the circuit, external resistance is added to limit the current surge.
The torque-speed characteristic of plugging braking shows that the braking torque remains nearly constant throughout the process.
Unlike regenerative braking, where energy is fed back to the power source, plugging braking dissipates excess energy as heat, making it less energy-efficient. However, it offers several advantages, such as faster braking than regenerative braking, simple implementation in both AC and DC motors, and no need for additional power sources.
Despite these benefits, plugging braking has its drawbacks. It leads to high energy wastage, as excess power is converted into heat, increasing wear and tear on motor components due to abrupt speed reversal. Additionally, it requires external resistance to avoid damaging the motor from excessive current.
Despite these limitations, plugging braking is widely used in cranes, lifts, machine tools, and emergency braking systems, where rapid stopping is necessary. Its ability to provide quick and effective braking makes it a preferred choice in industrial applications, despite its lower energy efficiency compared to regenerative braking.
3. Dynamic Braking
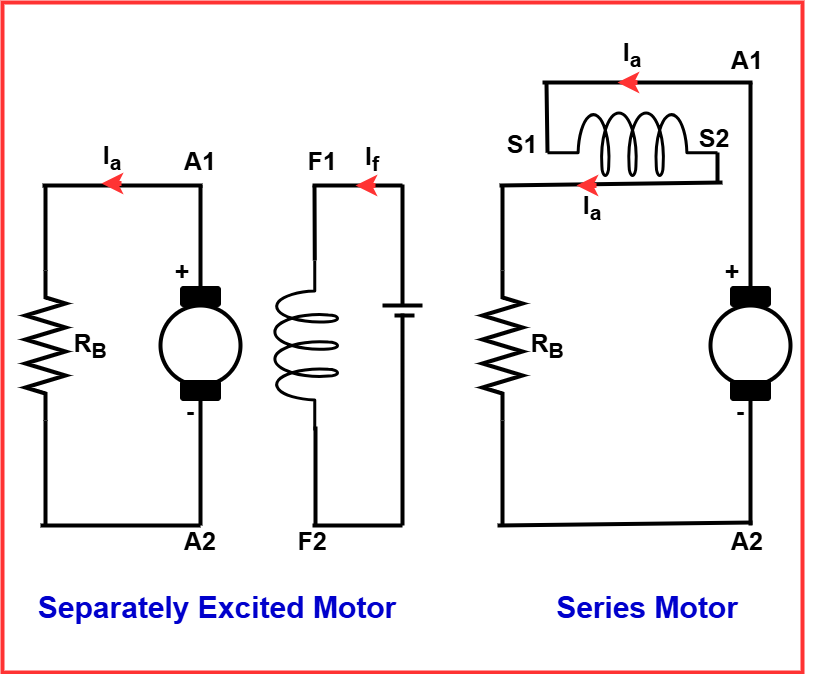
Dynamic Braking is a braking method where the motor is disconnected from its power source and connected to a resistor, allowing it to slow down by dissipating energy as heat. In this process, the rotating motor continues spinning due to inertia and begins acting as a self-excited generator. As a result, the generated current flows in the opposite direction, creating a counter torque that resists motion and decelerates the motor.
To ensure a smooth and controlled braking operation, external resistances are gradually adjusted, preventing sudden stops that could damage the system. Dynamic braking is widely used in electric trains, elevators, cranes, and industrial machinery, where rapid yet controlled deceleration is required. However, since the braking energy is converted into heat, energy recovery is not possible, making it less efficient than regenerative braking.
Dynamic braking offers several advantages, particularly when compared to plugging. One of its key benefits is that it eliminates the need for the power supply to provide additional energy for braking. This makes the process more efficient and reduces energy consumption while slowing down or stopping a motor. Additionally, it minimizes wear and tear on brake components by reducing reliance on friction-based braking systems. The regeneration process further enhances efficiency by decreasing the net energy used.
However, dynamic braking also has some disadvantages. During the braking process, the stored energy is dissipated as heat due to the resistance in the braking circuit and other connected components. This energy loss can impact overall system efficiency, making it less ideal in applications where energy conservation is a priority.
Despite these drawbacks, dynamic braking is widely used in various industrial applications where rapid or controlled stopping of DC motors is required. It is commonly found in systems such as fans, centrifuges, pumps, and conveyor belts, where quick deceleration and direction reversal are essential.
Additionally, dynamic braking is extensively utilized in transportation systems, including railcars, trolleybuses, electric trams, light rail vehicles, hybrid electric vehicles, and electric automobiles, ensuring smooth and efficient braking performance.
Advantages and Disadvantages of Electrical Braking
Electrical braking offers several advantages. It is a quick and cost-effective braking method that does not require any mechanical components, reducing wear and tear. Since there are no moving parts involved, maintenance is minimal, and the operation remains dust-free and clean.
One of its key benefits is that the energy generated during braking is converted back into electricity and returned to the supply network, improving efficiency. Additionally, electrical braking provides smooth, step-free braking, making it a simpler and more cost-effective solution. The use of closed-loop control allows for automatic regulation, further enhancing its performance.
However, electrical braking also has some limitations. It does not generate holding torque, meaning it cannot keep the motor in a fixed position after stopping. The choice of motors is also restricted, as they must have suitable braking characteristics. Furthermore, safety precautions must be carefully monitored to ensure safe operation. Another drawback is the increase in power consumption associated with electrical braking systems.
Conclusion
Braking is an essential process in electrical and mechanical systems, used to slow down or stop rotating machinery safely and efficiently. It plays a crucial role in controlling motor speed, preventing damage, and ensuring operational safety in various applications.
There are three primary types of electrical braking: Regenerative Braking, Plugging, and Dynamic Braking. Regenerative braking converts kinetic energy into electrical energy, which can be fed back into the power supply, improving efficiency. Plugging quickly stops the motor by reversing the supply terminals, but it wastes energy as heat. Dynamic braking uses resistors to dissipate excess energy, slowing down the motor without feeding energy back into the supply.
Each braking method has its advantages and limitations, and the choice depends on the specific application, efficiency requirements, and safety considerations. Understanding these braking techniques helps in optimizing motor performance in industrial machinery, electric vehicles, rail systems, and elevators, where controlled deceleration is critical.
Read Next: